What is a laser ceramic ring and how does it enhance the performance of laser cutting machines
A laser ceramic ring is a crucial component in laser cutting and welding machines, specifically within the laser head assembly.

A laser ceramic ring is a crucial component in laser cutting and welding machines, specifically within the laser head assembly. It acts as an insulator between the laser nozzle and the cutting head while ensuring precise alignment and stability. Made from high-performance ceramic materials, such as aluminum oxide (Al₂O₃) or zirconia (ZrO₂), these rings are known for their durability, heat resistance, and electrical insulation properties.
Functions of a Laser Ceramic Ring
-
Electrical Insulation
The ceramic ring prevents electrical interference between the nozzle and the laser head. This insulation is crucial for maintaining consistent laser performance, especially in high-power cutting applications. -
Thermal Stability
Since laser cutting involves high temperatures, the ceramic ring provides heat resistance, preventing damage to surrounding components. It ensures that the nozzle remains cool and functional, even during extended cutting operations. -
Precision and Alignment
A laser ceramic ring helps maintain the correct positioning of the nozzle in relation to the workpiece. Proper alignment is essential for achieving clean and precise cuts without distortions. -
Shock Absorption and Protection
The ceramic ring acts as a buffer, protecting the laser head from mechanical shocks and vibrations. This feature is particularly important in high-speed laser cutting, where stability affects accuracy. -
Facilitates Smooth Gas Flow
Assist gases, such as oxygen or nitrogen, pass through the laser nozzle to enhance cutting quality. The ceramic ring ensures optimal gas flow, minimizing turbulence and improving cutting efficiency.
Types of Laser Ceramic Rings
-
Standard Ceramic Rings
These are designed for general laser cutting applications and are compatible with most CO₂ and fiber laser machines. -
High-Density Ceramic Rings
Used in high-power laser systems, these rings offer superior durability and thermal resistance, making them ideal for demanding industrial applications. -
Customized Ceramic Rings
Some manufacturers offer tailor-made rings to fit specific laser cutting heads, optimizing performance for specialized cutting needs.
Advantages of Using Laser Ceramic Rings
- Enhanced Cutting Precision: Ensures the nozzle remains in perfect alignment, reducing errors in the cutting process.
- Increased Machine Lifespan: Protects sensitive components from heat and electrical interference, extending the overall lifespan of the laser system.
- Reduced Maintenance Costs: Durable ceramic rings require minimal replacement, lowering operational expenses.
- Improved Cutting Efficiency: Facilitates smooth gas flow, leading to cleaner cuts with fewer defects.
Maintenance and Replacement
To maintain optimal performance, laser ceramic rings should be regularly inspected for cracks or wear. A damaged ceramic ring can lead to misalignment, increased nozzle wear, and poor cutting quality. Replacing worn-out rings promptly ensures that the laser system operates at peak efficiency.
Conclusion
A laser ceramic ring is a vital component in laser cutting machines, providing insulation, thermal stability, and precision. Its role in ensuring smooth gas flow, preventing electrical interference, and protecting the nozzle makes it indispensable for high-quality laser cutting. Regular maintenance and choosing the right ceramic ring can significantly enhance the performance and longevity of a laser system.
What's Your Reaction?
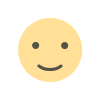
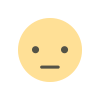
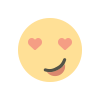

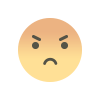
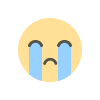
