From Concept to Creation: Blow Molding vs Injection Molding Explained
In the dynamic world of plastic manufacturing, the debate of blow molding vs injection molding continues to shape decisions for engineers, designers, and product developers.

In the world of plastic manufacturing, two of the most widely used processes are blow molding and injection molding. These techniques are crucial in shaping the vast array of plastic products we use every day—from water bottles and automotive parts to complex medical devices. While both methods rely on molding plastics, they have unique characteristics that make them suitable for different applications. Understanding the differences between blow molding vs injection molding is vital for manufacturers, designers, and even consumers who care about product quality and design efficiency.
Choosing the correct molding technique is not just a matter of preference but one of functionality, cost, and end-use requirements. The wrong choice can result in increased expenses, poor product performance, or failed production runs. Therefore, having a clear understanding of blow molding vs injection molding helps ensure that projects move seamlessly from concept to creation. In this article, we'll break down the definitions, key differences, applications, advantages, and decision-making considerations for each process.
Understanding the Basics: What Are Blow Molding and Injection Molding?
Blow molding is a manufacturing process used to create hollow plastic parts such as bottles, containers, and tanks. The process involves melting down plastic and forming it into a parison (a tube-like piece of plastic with a hole at one end). The parison is then clamped into a mold and inflated with air until it takes the shape of the mold cavity. There are three main types of blow molding: extrusion blow molding, injection blow molding, and stretch blow molding, each suitable for different product requirements and material specifications.
Injection molding, on the other hand, is a process designed to produce solid plastic parts with high precision. In this technique, melted plastic is injected under high pressure into a steel mold cavity. Once the plastic cools and solidifies, the mold opens to eject the final product. Injection molding is ideal for producing detailed components with complex geometries, including electronic housings, automotive dashboards, and household appliances. The main advantage lies in its ability to produce consistent, high-quality parts in large volumes with minimal waste.
Key Differences in Process and Design Considerations
When comparing blow molding vs injection molding, the most significant difference lies in the type of products each method can create. Blow molding is specifically used to make hollow parts, which makes it ideal for containers, bottles, and tanks. These parts typically require a uniform wall thickness and are lighter in weight. The tooling and mold design in blow molding are generally simpler and less expensive because the mold only shapes the outer surface of the part.
Injection molding is much more precise and is typically used for solid, complex components. The molds used in injection molding are more intricate and expensive to manufacture because they must form both the external and internal features of the product. This process allows for a wider range of design possibilities, including parts with multiple cavities, inserts, and undercuts. As a result, injection molding is preferred when detail, strength, and consistency are of paramount importance.
Applications: When to Use Each Molding Process
The choice between blow molding vs injection molding is largely determined by the end-use application of the product. Blow molding is commonly used in industries where lightweight and hollow containers are required. For example, the beverage and packaging industries rely heavily on blow molding to manufacture PET bottles and plastic jugs. Similarly, the automotive sector uses blow molding for producing ducts, fuel tanks, and reservoirs that require hollow designs.
Injection molding, due to its superior precision and structural integrity, is favored in sectors such as consumer electronics, medical devices, and automotive interiors. It is ideal for parts that must withstand mechanical stress or require a tight tolerance fit. Examples include smartphone casings, syringes, gears, and dashboard components. The repeatability of injection molding makes it an excellent choice for producing identical parts in mass quantities with minimal variance.
Advantages and Limitations of Each Molding Technique
Each molding technique comes with its own set of advantages and limitations that affect production efficiency, cost, and product quality. Blow molding is highly efficient for producing large volumes of hollow items at a lower cost per unit. It offers faster cycle times and requires less raw material, making it more sustainable for certain types of products. However, it lacks the precision and design complexity that injection molding can achieve. Additionally, wall thickness and part consistency may vary slightly with blow molding, which can impact performance for critical applications.
Injection molding offers superior precision and the ability to produce complex parts with high strength and durability. It supports a wide range of materials, including thermoplastics, thermosets, and elastomers. The downsides include higher tooling costs and longer lead times, particularly for prototyping and mold design. The process also generates more waste material, especially when using runners and sprues, although some of this can be recycled. Ultimately, the choice between blow molding vs injection molding depends on the project's specific requirements.
Choosing the Right Molding Method for Your Project
Selecting between blow molding vs injection molding starts with understanding your product's function, design, and required volume. If your product is hollow, lightweight, and doesn't need high precision—such as bottles or tanks—blow molding is likely the better option. Its lower tooling cost and faster production cycle make it ideal for high-volume consumer goods. Conversely, if your product requires fine details, complex geometry, or structural integrity, injection molding is the optimal choice despite its higher upfront costs.
Cost is another major factor to consider. Injection molding demands a higher initial investment due to the complexity of mold design, but it offers excellent scalability and repeatability over long runs. Blow molding has a lower cost of entry and is best suited for simpler shapes and large production volumes. Prototyping, testing, and consultation with a manufacturing expert can help validate your choice. Ultimately, understanding the core differences between blow molding vs injection molding ensures that your concept transforms into a functional and cost-effective product.
Conclusion
In the dynamic world of plastic manufacturing, the debate of blow molding vs injection molding continues to shape decisions for engineers, designers, and product developers. Each technique offers unique benefits tailored to different applications, budgets, and production scales. Blow molding stands out for hollow, lightweight products with low tooling costs, while injection molding excels in producing complex, high-precision parts with unmatched consistency.
Choosing the right method begins with a clear understanding of your product’s design goals, functional requirements, and budget constraints. From concept to creation, the journey of manufacturing plastic parts becomes significantly smoother when armed with knowledge about molding techniques. Whether you're launching a new consumer product or streamlining a production line, your awareness of blow molding vs injection molding could be the key to success.
What's Your Reaction?
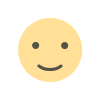
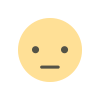
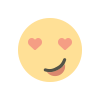

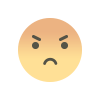
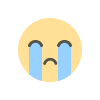
